Destylator przemysłowy to urządzenie, które służy do separacji cieczy na podstawie różnicy w temperaturach wrzenia. Proces destylacji jest kluczowy w wielu branżach, takich jak chemiczna, petrochemiczna czy spożywcza. W przypadku destylacji, ciecz jest podgrzewana do momentu, gdy zaczyna parować, a następnie para jest schładzana i skraplana z powrotem do formy cieczy. Dzięki temu możliwe jest oddzielenie składników o różnych temperaturach wrzenia. W przemyśle chemicznym destylatory są wykorzystywane do oczyszczania rozpuszczalników oraz produkcji różnych substancji chemicznych. W branży spożywczej destylacja jest stosowana do produkcji alkoholu, gdzie fermentowane surowce są poddawane procesowi destylacji w celu uzyskania wysokoprocentowego napoju. W przemyśle naftowym destylatory służą do rozdzielania frakcji ropy naftowej, co pozwala na uzyskanie paliw oraz innych produktów petrochemicznych.
Jakie są rodzaje destylatorów przemysłowych i ich cechy
W przemyśle istnieje wiele rodzajów destylatorów, które różnią się konstrukcją oraz zastosowaniem. Najpopularniejsze z nich to destylatory prostokątne, kolumnowe oraz wirówkowe. Destylatory prostokątne są najprostsze w budowie i najczęściej stosowane w małych zakładach produkcyjnych. Działają na zasadzie prostego podgrzewania cieczy i zbierania pary w górnej części urządzenia. Z kolei destylatory kolumnowe są bardziej zaawansowane technologicznie i pozwalają na uzyskanie wyższej czystości produktu końcowego. W tego typu urządzeniach para przechodzi przez kolumnę, w której zachodzi wielokrotna kondensacja i odparowanie, co sprzyja lepszemu rozdzieleniu składników. Destylatory wirówkowe natomiast wykorzystują siłę odśrodkową do separacji cieczy, co czyni je idealnymi do procesów wymagających dużych prędkości obrotowych.
Jakie są kluczowe elementy konstrukcyjne destylatora przemysłowego
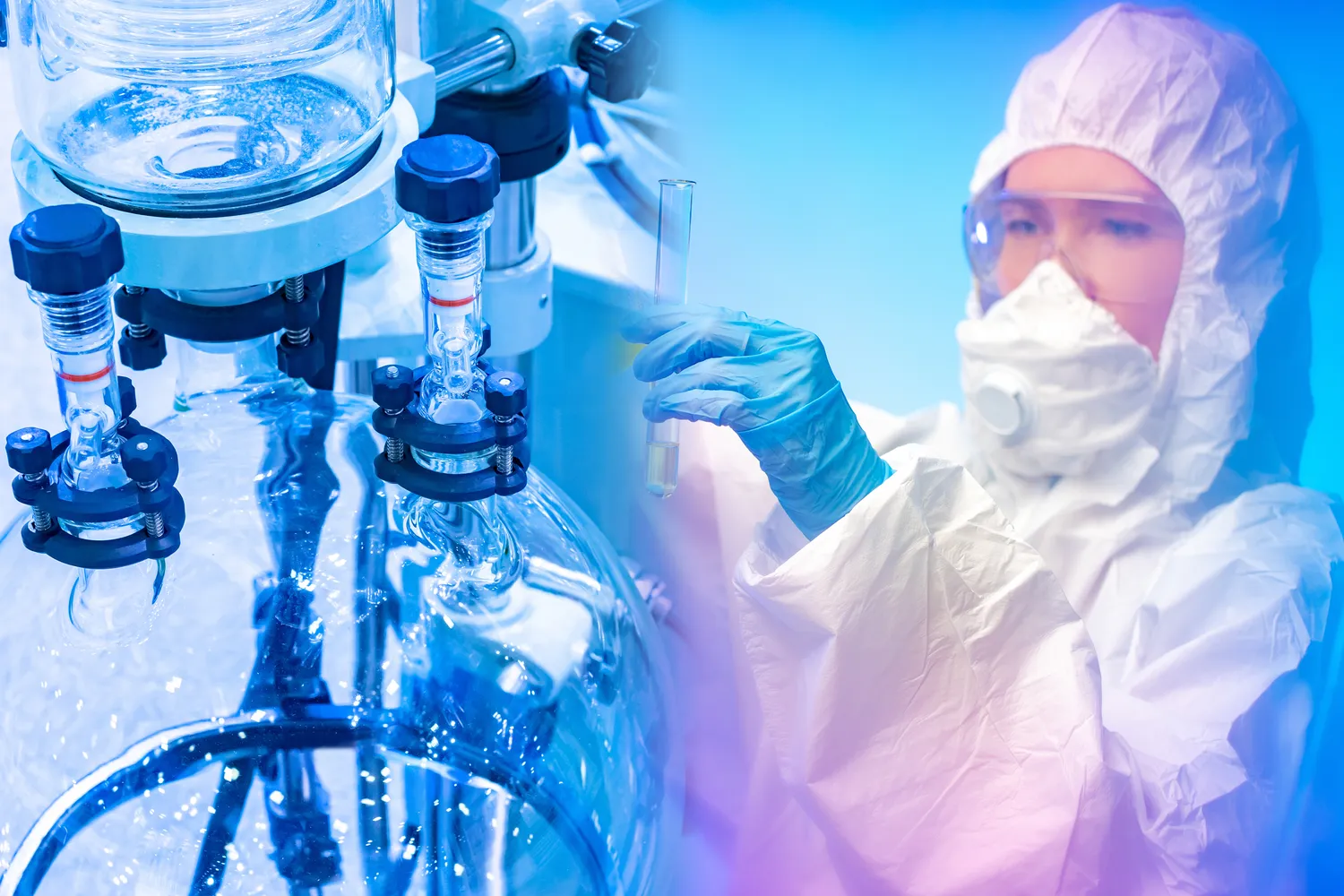
Konstrukcja destylatora przemysłowego składa się z kilku kluczowych elementów, które mają istotny wpływ na jego funkcjonowanie oraz efektywność procesu destylacji. Najważniejszym elementem jest zbiornik, w którym znajduje się ciecz poddawana procesowi destylacji. Zbiornik ten musi być wykonany z materiałów odpornych na wysokie temperatury oraz korozję. Kolejnym istotnym elementem jest system grzewczy, który może być oparty na różnych źródłach energii, takich jak elektryczność czy para wodna. Ważnym komponentem jest również kolumna destylacyjna, która umożliwia wielokrotne skraplanie i odparowywanie pary, co zwiększa efektywność procesu rozdzielania składników. Dodatkowo, każdy destylator wyposażony jest w system chłodzenia, który pozwala na skraplanie pary z powrotem do formy cieczy. Oprócz tego niezbędne są także zawory kontrolujące przepływ cieczy oraz systemy monitorujące temperaturę i ciśnienie wewnątrz urządzenia.
Jakie są zalety stosowania nowoczesnych destylatorów przemysłowych
Nowoczesne destylatory przemysłowe oferują szereg zalet, które przyczyniają się do zwiększenia efektywności procesów produkcyjnych oraz poprawy jakości uzyskiwanych produktów. Przede wszystkim nowoczesne technologie pozwalają na automatyzację procesów, co znacząco redukuje czas potrzebny na przeprowadzenie całej operacji destylacji. Automatyczne systemy monitorowania i kontroli parametrów pracy urządzenia zapewniają stabilność procesu oraz minimalizują ryzyko błędów ludzkich. Ponadto nowoczesne destylatory charakteryzują się wyższą efektywnością energetyczną, co przekłada się na mniejsze koszty eksploatacyjne oraz mniejszy wpływ na środowisko naturalne. Dodatkowo innowacyjne rozwiązania technologiczne umożliwiają osiąganie wyższej czystości produktów końcowych, co jest szczególnie istotne w branżach wymagających wysokiej jakości surowców.
Jakie są najczęstsze problemy związane z destylatorami przemysłowymi
Podczas eksploatacji destylatorów przemysłowych mogą występować różnorodne problemy, które wpływają na ich wydajność oraz jakość uzyskiwanych produktów. Jednym z najczęstszych problemów jest osadzanie się zanieczyszczeń w zbiorniku oraz kolumnie destylacyjnej, co może prowadzić do zmniejszenia efektywności procesu destylacji. Zanieczyszczenia te mogą pochodzić z surowców wykorzystywanych w procesie lub być wynikiem reakcji chemicznych zachodzących w trakcie destylacji. Innym istotnym problemem jest nieprawidłowe ustawienie parametrów pracy urządzenia, takich jak temperatura czy ciśnienie, co może prowadzić do niepełnego rozdzielenia składników oraz obniżenia jakości produktu końcowego. Warto również zwrócić uwagę na kwestie związane z systemem chłodzenia, który może ulegać awariom, co skutkuje brakiem odpowiedniego skraplania pary. Dodatkowo, niewłaściwe zarządzanie procesem może prowadzić do nadmiernego zużycia energii oraz zwiększenia kosztów produkcji.
Jakie są koszty inwestycji w destylatory przemysłowe
Koszty inwestycji w destylatory przemysłowe mogą się znacznie różnić w zależności od wielu czynników, takich jak rodzaj urządzenia, jego wydajność oraz zastosowane technologie. Na początku warto zwrócić uwagę na cenę zakupu samego destylatora, która może wynosić od kilku tysięcy do nawet milionów złotych w przypadku dużych i zaawansowanych technologicznie systemów. Oprócz kosztu zakupu należy uwzględnić także koszty instalacji oraz uruchomienia urządzenia, które mogą obejmować prace budowlane, elektryczne oraz hydrauliczne. Kolejnym istotnym elementem są koszty eksploatacyjne, które obejmują zużycie energii, konserwację oraz ewentualne naprawy. Warto również pamiętać o kosztach związanych z surowcami wykorzystywanymi w procesie destylacji, które mogą znacząco wpłynąć na rentowność całego przedsięwzięcia.
Jakie są trendy w rozwoju technologii destylacji przemysłowej
W ostatnich latach obserwuje się dynamiczny rozwój technologii związanych z destylacją przemysłową, co ma na celu zwiększenie efektywności procesów produkcyjnych oraz minimalizację wpływu na środowisko. Jednym z kluczowych trendów jest automatyzacja procesów destylacji, która pozwala na precyzyjne sterowanie parametrami pracy urządzeń oraz monitorowanie ich wydajności w czasie rzeczywistym. Dzięki zastosowaniu nowoczesnych systemów informatycznych możliwe jest optymalizowanie procesów produkcyjnych oraz redukcja błędów ludzkich. Kolejnym istotnym trendem jest rozwój technologii odzysku ciepła, co pozwala na zmniejszenie zużycia energii oraz obniżenie kosztów eksploatacyjnych. Wiele firm inwestuje również w badania nad nowymi materiałami konstrukcyjnymi, które charakteryzują się lepszą odpornością na wysokie temperatury i korozję. Równocześnie rośnie zainteresowanie ekologicznymi rozwiązaniami, takimi jak wykorzystanie odnawialnych źródeł energii czy recykling odpadów powstających podczas procesu destylacji.
Jakie są wymagania dotyczące bezpieczeństwa przy obsłudze destylatorów
Bezpieczeństwo przy obsłudze destylatorów przemysłowych jest kluczowym aspektem, który należy uwzględnić zarówno podczas projektowania urządzeń, jak i ich eksploatacji. Pracownicy obsługujący destylatory muszą być odpowiednio przeszkoleni i świadomi zagrożeń związanych z pracą z substancjami chemicznymi oraz wysokimi temperaturami. W pierwszej kolejności należy zapewnić odpowiednią wentylację pomieszczeń, w których znajdują się destylatory, aby uniknąć gromadzenia się szkodliwych oparów. Ważne jest również stosowanie odpowiednich środków ochrony osobistej, takich jak rękawice czy okulary ochronne. Kolejnym istotnym elementem jest regularne przeprowadzanie inspekcji technicznych urządzeń oraz ich konserwacja zgodnie z zaleceniami producenta. Należy także wdrożyć procedury awaryjne na wypadek wystąpienia niebezpiecznych sytuacji, takich jak wycieki substancji chemicznych czy pożary.
Jakie są najlepsze praktyki dotyczące konserwacji destylatorów przemysłowych
Aby zapewnić długotrwałe i efektywne działanie destylatorów przemysłowych, kluczowe jest przestrzeganie najlepszych praktyk dotyczących ich konserwacji. Regularne przeglądy techniczne powinny być przeprowadzane zgodnie z harmonogramem ustalonym przez producenta urządzenia. W ramach tych przeglądów warto zwrócić szczególną uwagę na stan zbiornika oraz kolumny destylacyjnej, a także sprawdzić szczelność wszystkich połączeń i zaworów. Dodatkowo ważne jest czyszczenie elementów wewnętrznych urządzenia z osadów i zanieczyszczeń, które mogą wpływać na wydajność procesu destylacji. Warto również monitorować parametry pracy urządzenia takie jak temperatura czy ciśnienie, aby szybko reagować na ewentualne odchylenia od normy. Utrzymanie odpowiednich warunków pracy dla systemu chłodzenia jest równie istotne – regularna kontrola poziomu czynnika chłodniczego oraz sprawdzenie stanu wymienników ciepła mogą zapobiec awariom i zwiększyć efektywność całego procesu.
Jakie są różnice między małymi a dużymi destylatorami przemysłowymi
Różnice między małymi a dużymi destylatorami przemysłowymi dotyczą wielu aspektów związanych z ich konstrukcją, wydajnością oraz zastosowaniem. Małe destylatory często charakteryzują się prostszą budową i niższymi kosztami zakupu oraz eksploatacji. Są one idealnym rozwiązaniem dla niewielkich zakładów produkcyjnych lub laboratorium zajmujących się badaniami i rozwojem nowych produktów. Zazwyczaj mają one mniejsze moce przerobowe i są bardziej elastyczne pod względem dostosowywania do różnych procesów produkcyjnych. Z kolei duże destylatory przemysłowe są zazwyczaj bardziej skomplikowane technologicznie i wymagają znacznych inwestycji finansowych zarówno przy zakupie, jak i podczas eksploatacji. Charakteryzują się one wysoką wydajnością i są zdolne do przetwarzania dużych ilości surowców w krótkim czasie. Często są wyposażone w zaawansowane systemy automatyzacji oraz monitorowania procesów produkcyjnych.