Destylacja rozpuszczalników to proces, który polega na oddzieleniu składników mieszaniny na podstawie różnic w ich temperaturach wrzenia. Jest to jedna z najstarszych i najczęściej stosowanych metod separacji substancji chemicznych. W procesie tym wykorzystuje się fakt, że różne substancje mają różne temperatury wrzenia, co pozwala na ich skuteczne oddzielenie. W praktyce destylacja odbywa się w specjalnych aparaturach zwanych destylatorami, które mogą mieć różną budowę i zastosowanie. W przypadku destylacji prostych mieszanin, takich jak woda i alkohol, proces ten jest stosunkowo łatwy do przeprowadzenia. Jednak w przypadku bardziej skomplikowanych mieszanin, konieczne może być zastosowanie destylacji frakcyjnej, która pozwala na oddzielenie wielu składników jednocześnie. Kluczowym elementem tego procesu jest również odpowiedni dobór warunków pracy, takich jak ciśnienie czy temperatura, które mają znaczący wpływ na efektywność separacji.
Jakie są zastosowania destylacji rozpuszczalników w przemyśle
Destylacja rozpuszczalników znajduje szerokie zastosowanie w różnych gałęziach przemysłu, od chemicznego po farmaceutyczny. Proces ten jest kluczowy w produkcji wielu substancji chemicznych, w tym rozpuszczalników organicznych, alkoholi oraz olejków eterycznych. W przemyśle chemicznym destylacja jest często wykorzystywana do oczyszczania surowców oraz do odzyskiwania cennych składników z odpadów produkcyjnych. Na przykład w produkcji alkoholu etylowego destylacja pozwala na uzyskanie wysokiej czystości trunku poprzez usunięcie niepożądanych związków. W przemyśle farmaceutycznym destylacja jest stosowana do oczyszczania substancji czynnych oraz do produkcji rozpuszczalników używanych w procesach syntezy chemicznej. Dodatkowo destylacja jest również wykorzystywana w przemyśle petrochemicznym do separacji różnych frakcji ropy naftowej, co ma kluczowe znaczenie dla produkcji paliw i innych produktów naftowych.
Jakie są różnice między destylacją prostą a frakcyjną
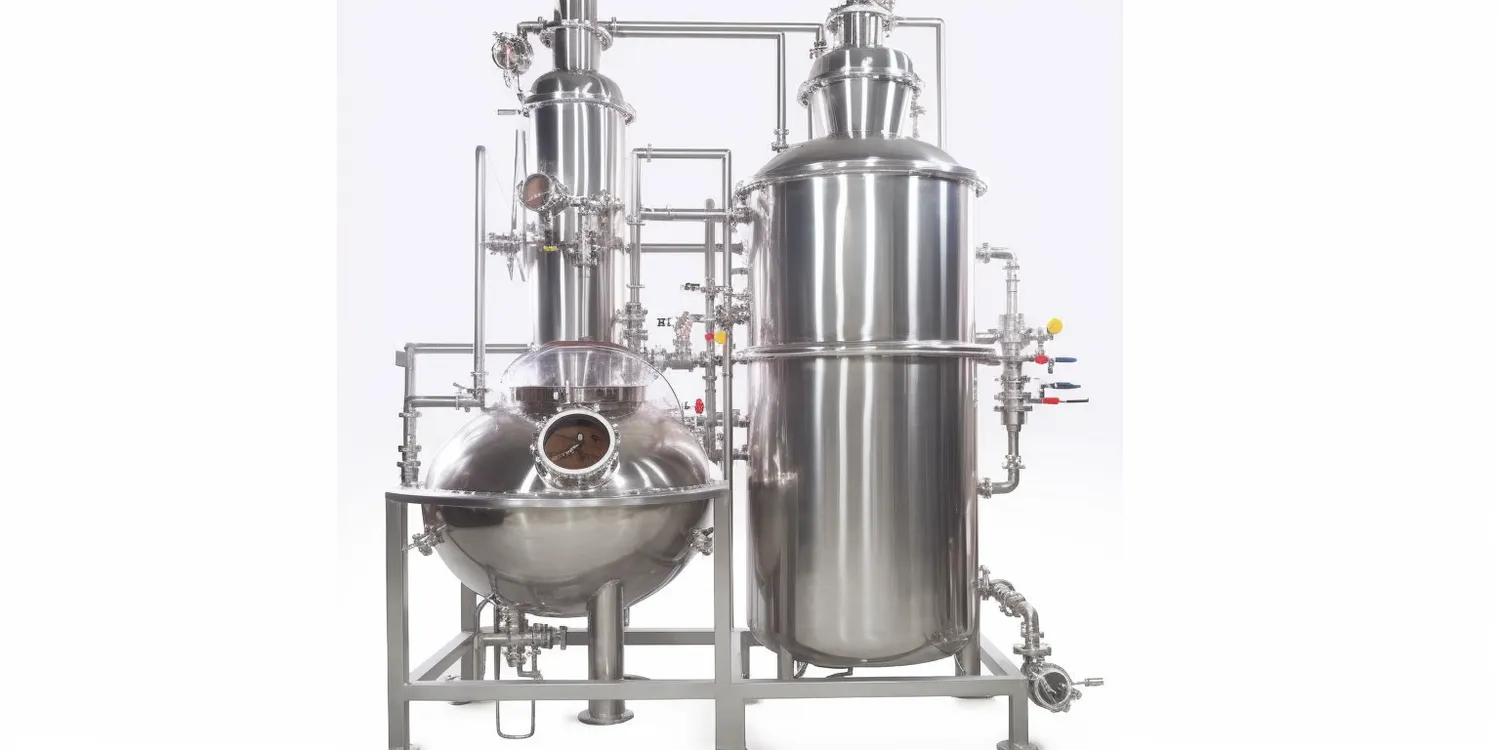
Destylacja prosta i frakcyjna to dwa podstawowe rodzaje procesów destylacyjnych, które różnią się zarówno pod względem konstrukcji aparatury, jak i zastosowania. Destylacja prosta jest najprostszą formą tego procesu i polega na jednorazowym podgrzewaniu mieszaniny oraz zbieraniu pary kondensującej się w chłodnicy. Jest ona skuteczna głównie w przypadku mieszanin składających się z dwóch składników o znacznie różnych temperaturach wrzenia. Natomiast destylacja frakcyjna jest bardziej zaawansowaną techniką, która umożliwia oddzielanie wielu składników jednocześnie dzięki zastosowaniu kolumny frakcyjnej. Kolumna ta zawiera elementy takie jak talerze czy packing, które zwiększają powierzchnię kontaktu między parą a cieczą, co pozwala na wielokrotne skraplanie i parowanie substancji. Dzięki temu możliwe jest uzyskanie wyższej czystości poszczególnych frakcji oraz lepsza separacja składników o zbliżonych temperaturach wrzenia.
Jakie są najczęstsze problemy podczas destylacji rozpuszczalników
Podczas przeprowadzania procesu destylacji rozpuszczalników mogą wystąpić różne problemy techniczne, które mogą wpłynąć na efektywność separacji oraz jakość uzyskiwanych produktów. Jednym z najczęstszych problemów jest tzw. „przegrzewanie” cieczy roboczej, które może prowadzić do niekontrolowanego wzrostu temperatury i powstawania niepożądanych produktów ubocznych. Innym istotnym problemem jest tworzenie się piany podczas gotowania cieczy, co może prowadzić do zanieczyszczenia kondensatu oraz obniżenia wydajności procesu. Ponadto niewłaściwe ustawienia parametrów pracy urządzenia, takich jak ciśnienie czy temperatura, mogą prowadzić do nieskutecznej separacji składników lub ich niepełnego odzysku. Ważne jest także monitorowanie jakości surowców używanych w procesie oraz regularne czyszczenie aparatury, aby uniknąć osadów i zanieczyszczeń wpływających na wyniki destylacji.
Jakie są kluczowe czynniki wpływające na efektywność destylacji rozpuszczalników
Efektywność procesu destylacji rozpuszczalników zależy od wielu czynników, które mogą znacząco wpłynąć na jakość uzyskiwanych produktów oraz wydajność całego procesu. Pierwszym z tych czynników jest temperatura, która musi być odpowiednio dobrana do charakterystyki mieszaniny. Zbyt niska temperatura może prowadzić do niepełnej separacji składników, podczas gdy zbyt wysoka może powodować degradację niektórych substancji. Kolejnym istotnym czynnikiem jest ciśnienie, które również ma wpływ na temperatury wrzenia poszczególnych składników. W przypadku destylacji frakcyjnej, konstrukcja kolumny frakcyjnej oraz jej wysokość mają kluczowe znaczenie dla efektywności separacji. Im wyższa kolumna, tym większa powierzchnia kontaktu między parą a cieczą, co pozwala na lepsze oddzielenie składników o zbliżonych temperaturach wrzenia. Ważne jest także odpowiednie dobranie materiałów użytych w aparaturze, ponieważ różne materiały mogą reagować z substancjami chemicznymi i wpływać na jakość końcowego produktu.
Jakie są najpopularniejsze metody oczyszczania rozpuszczalników po destylacji
Oczyszczanie rozpuszczalników po procesie destylacji jest kluczowym etapem, który ma na celu usunięcie wszelkich zanieczyszczeń oraz poprawę jakości końcowego produktu. Istnieje kilka popularnych metod oczyszczania, które można zastosować w zależności od rodzaju zanieczyszczeń oraz specyfiki rozpuszczalnika. Jedną z najczęściej stosowanych metod jest filtracja, która pozwala na usunięcie stałych cząstek oraz osadów powstałych podczas destylacji. W przypadku rozpuszczalników organicznych, często stosuje się również adsorpcję na węglu aktywnym lub innych materiałach adsorpcyjnych, co pozwala na usunięcie niepożądanych związków chemicznych. Inną metodą jest ekstrakcja cieczy, która polega na wykorzystaniu innego rozpuszczalnika do selektywnego wydobycia zanieczyszczeń. Dodatkowo, w niektórych przypadkach można zastosować krystalizację lub rektyfikację jako metody oczyszczania. Ostateczny wybór metody zależy od specyfiki danej aplikacji oraz wymagań dotyczących czystości końcowego produktu.
Jakie są różnice w destylacji rozpuszczalników organicznych i nieorganicznych
Destylacja rozpuszczalników organicznych i nieorganicznych różni się pod wieloma względami, co wynika głównie z ich odmiennych właściwości fizykochemicznych. Rozpuszczalniki organiczne, takie jak alkohole czy ketony, często mają niższe temperatury wrzenia w porównaniu do wielu rozpuszczalników nieorganicznych, takich jak sole czy kwasy mineralne. To sprawia, że proces destylacji organicznych substancji może być prostszy i mniej wymagający pod względem technologicznym. Jednakże organiczne rozpuszczalniki mogą być bardziej podatne na reakcje chemiczne podczas podgrzewania, co wymaga szczególnej uwagi przy doborze warunków pracy. Z drugiej strony, destylacja rozpuszczalników nieorganicznych często wiąże się z wyższymi temperaturami oraz koniecznością stosowania specjalistycznych materiałów odpornych na korozję i wysokie ciśnienie. Dodatkowo w przypadku substancji nieorganicznych może występować ryzyko tworzenia się osadów lub reakcji ze składnikami aparatury.
Jakie są nowoczesne technologie wykorzystywane w destylacji rozpuszczalników
W ostatnich latach rozwój technologii związanych z destylacją rozpuszczalników przyniósł wiele innowacyjnych rozwiązań, które znacząco poprawiły efektywność tego procesu. Jednym z najważniejszych trendów jest automatyzacja procesów destylacyjnych, która pozwala na precyzyjne monitorowanie i kontrolowanie parametrów pracy urządzeń. Dzięki zastosowaniu nowoczesnych systemów sterowania możliwe jest optymalizowanie warunków pracy w czasie rzeczywistym, co przekłada się na lepszą jakość uzyskiwanych produktów oraz zwiększenie wydajności procesu. Kolejnym innowacyjnym rozwiązaniem są kolumny frakcyjne o wysokiej wydajności, które umożliwiają skuteczną separację składników o bliskich temperaturach wrzenia dzięki zastosowaniu zaawansowanych materiałów i konstrukcji. Ponadto rozwijają się technologie membranowe oraz ekstrakcyjne, które stanowią alternatywę dla tradycyjnej destylacji i mogą być stosowane w przypadku trudnych do separacji mieszanin.
Jakie są przyszłe kierunki badań nad destylacją rozpuszczalników
Przyszłość badań nad destylacją rozpuszczalników koncentruje się na kilku kluczowych obszarach, które mają potencjał przynieść znaczące innowacje w tej dziedzinie. Jednym z głównych kierunków jest rozwój bardziej efektywnych technologii separacyjnych opartych na nowych materiałach i konstrukcjach aparatury. Badania nad nanomateriałami oraz ich zastosowaniem w procesach destylacyjnych mogą prowadzić do znacznego zwiększenia wydajności separacji oraz poprawy jakości uzyskiwanych produktów. Kolejnym istotnym obszarem badań jest integracja procesów chemicznych z technologią destylacyjną w celu osiągnięcia synergii między różnymi etapami produkcji chemicznej. Może to przyczynić się do zmniejszenia kosztów operacyjnych oraz zwiększenia efektywności energetycznej procesów przemysłowych. Również rosnące zainteresowanie ekologicznymi aspektami produkcji chemicznej skłania naukowców do poszukiwania bardziej zrównoważonych metod oczyszczania i odzysku rozpuszczalników, które będą miały mniejszy wpływ na środowisko naturalne.
Jakie są wyzwania związane z destylacją rozpuszczalników w przemyśle
W przemyśle destylacja rozpuszczalników wiąże się z wieloma wyzwaniami, które mogą wpływać na efektywność i bezpieczeństwo procesu. Jednym z kluczowych problemów jest zarządzanie dużymi ilościami odpadów powstających podczas destylacji, co wymaga wdrożenia skutecznych strategii ich utylizacji lub recyklingu. Wiele rozpuszczalników jest substancjami toksycznymi lub łatwopalnymi, co stawia wysokie wymagania dotyczące bezpieczeństwa pracy oraz ochrony środowiska. Ponadto, zmieniające się przepisy dotyczące ochrony środowiska oraz normy jakościowe mogą wymuszać na przedsiębiorstwach dostosowywanie procesów destylacyjnych do nowych regulacji. Wyzwania te często prowadzą do konieczności inwestycji w nowoczesne technologie oraz szkolenie personelu, aby zapewnić zgodność z obowiązującymi standardami. Również zmniejszające się zasoby surowców naturalnych oraz rosnące koszty energii stawiają przed przemysłem nowe zadania, które wymagają innowacyjnych rozwiązań.