Budowa maszyn pneumatycznych opiera się na kilku kluczowych elementach, które współpracują ze sobą, aby zapewnić efektywne działanie systemu. Podstawowym składnikiem jest sprężarka, która odpowiada za wytwarzanie sprężonego powietrza. Sprężarki mogą być różnego rodzaju, w tym tłokowe, śrubowe czy wirnikowe, a ich wybór zależy od specyficznych potrzeb aplikacji. Kolejnym istotnym elementem są zbiorniki na sprężone powietrze, które gromadzą energię i umożliwiają jej wykorzystanie w odpowiednich momentach. W systemie pneumatycznym niezbędne są również zawory sterujące, które regulują przepływ powietrza oraz ciśnienie w układzie. Zawory te mogą być ręczne lub automatyczne, co pozwala na dostosowanie działania maszyny do wymagań produkcyjnych. Oprócz tego istotnymi komponentami są siłowniki pneumatyczne, które przekształcają energię sprężonego powietrza w ruch mechaniczny. Siłowniki te dzielą się na różne typy, takie jak cylindry jednostronnego lub dwustronnego działania.
Jakie są zalety i wady maszyn pneumatycznych
Maszyny pneumatyczne mają wiele zalet, które przyczyniają się do ich popularności w różnych branżach przemysłowych. Jedną z głównych korzyści jest ich prostota konstrukcji oraz łatwość w obsłudze. Dzięki temu operatorzy mogą szybko nauczyć się pracy z takimi urządzeniami. Ponadto maszyny pneumatyczne charakteryzują się dużą niezawodnością i długowiecznością, co sprawia, że są one opłacalną inwestycją dla firm. Kolejną zaletą jest ich zdolność do pracy w trudnych warunkach, takich jak wysokie temperatury czy obecność substancji chemicznych, co czyni je idealnym rozwiązaniem dla przemysłu chemicznego czy spożywczego. Niemniej jednak istnieją również pewne wady związane z użytkowaniem maszyn pneumatycznych. Przede wszystkim koszt sprężonego powietrza może być znaczny, zwłaszcza w przypadku dużych instalacji. Dodatkowo systemy te wymagają regularnej konserwacji oraz monitorowania ciśnienia, co wiąże się z dodatkowymi kosztami operacyjnymi.
Jakie zastosowania mają maszyny pneumatyczne w przemyśle
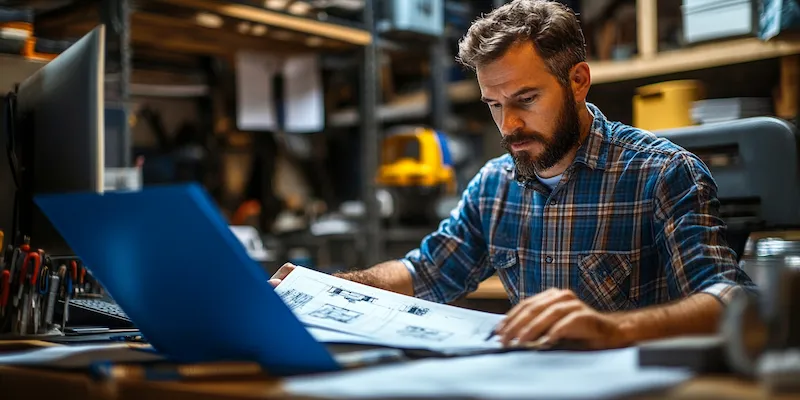
Maszyny pneumatyczne znajdują szerokie zastosowanie w różnych dziedzinach przemysłu dzięki swojej wszechstronności i efektywności. W przemyśle motoryzacyjnym często wykorzystuje się je do montażu i demontażu części samochodowych, gdzie precyzyjne i szybkie działanie jest kluczowe dla wydajności produkcji. W branży spożywczej maszyny pneumatyczne służą do transportu materiałów sypkich oraz pakowania produktów, co zapewnia zachowanie higieny i bezpieczeństwa żywności. W przemyśle elektronicznym technologia ta jest wykorzystywana do precyzyjnego montażu podzespołów elektronicznych oraz testowania urządzeń. Ponadto maszyny pneumatyczne są powszechnie stosowane w systemach automatyki przemysłowej do sterowania procesami produkcyjnymi oraz manipulacji materiałami. W sektorze budowlanym znajdują zastosowanie w narzędziach takich jak młoty udarowe czy wiertnice pneumatyczne, które ułatwiają wykonywanie prac budowlanych.
Jakie są najnowsze trendy w budowie maszyn pneumatycznych
W ostatnich latach można zaobserwować wiele interesujących trendów związanych z budową maszyn pneumatycznych, które mają na celu poprawę ich wydajności oraz efektywności energetycznej. Jednym z kluczowych kierunków rozwoju jest automatyzacja procesów produkcyjnych poprzez integrację maszyn pneumatycznych z systemami sterowania opartymi na sztucznej inteligencji i Internet of Things (IoT). Dzięki temu możliwe jest monitorowanie pracy urządzeń w czasie rzeczywistym oraz optymalizacja ich działania na podstawie analizy danych. Kolejnym ważnym trendem jest miniaturyzacja komponentów pneumatycznych, co pozwala na tworzenie bardziej kompaktowych i wydajnych układów. Wprowadzenie nowych materiałów oraz technologii produkcji przyczynia się także do zwiększenia trwałości i niezawodności tych maszyn. Również ekologia staje się coraz ważniejszym aspektem przy projektowaniu maszyn pneumatycznych; producenci starają się ograniczać zużycie energii oraz emisję hałasu poprzez rozwój bardziej efektywnych sprężarek i zaworów.
Jakie są kluczowe różnice między maszynami pneumatycznymi a hydraulicznymi
Maszyny pneumatyczne i hydrauliczne to dwa różne systemy, które służą do przekształcania energii w ruch mechaniczny, jednak różnią się one zasadniczo pod względem działania oraz zastosowań. Główną różnicą jest medium robocze; w systemach pneumatycznych wykorzystywane jest sprężone powietrze, podczas gdy w hydraulicznych stosuje się ciecz, najczęściej olej. Ta różnica wpływa na wiele aspektów ich funkcjonowania. Maszyny pneumatyczne są zazwyczaj lżejsze i bardziej kompaktowe, co sprawia, że są łatwiejsze w instalacji i mobilności. Z drugiej strony, systemy hydrauliczne oferują znacznie większą siłę i precyzję, co czyni je idealnym rozwiązaniem w aplikacjach wymagających dużych obciążeń, takich jak prace budowlane czy przemysł ciężki. W kontekście kosztów eksploatacji, sprężone powietrze może być droższe niż olej hydrauliczny, co wpływa na wybór technologii w danym zastosowaniu. Kolejnym istotnym aspektem jest bezpieczeństwo; maszyny pneumatyczne są mniej podatne na wycieki i związane z nimi zagrożenia środowiskowe, podczas gdy systemy hydrauliczne mogą stwarzać ryzyko zanieczyszczenia w przypadku awarii.
Jakie są kluczowe zasady dotyczące konserwacji maszyn pneumatycznych
Konserwacja maszyn pneumatycznych jest kluczowym elementem zapewniającym ich długotrwałe i efektywne działanie. Regularne przeglądy oraz odpowiednia pielęgnacja komponentów mogą znacząco wydłużyć żywotność urządzeń oraz zminimalizować ryzyko awarii. Podstawową zasadą jest regularna kontrola ciśnienia sprężonego powietrza w układzie; niewłaściwe ciśnienie może prowadzić do uszkodzenia elementów lub obniżenia wydajności maszyny. Ważne jest również monitorowanie jakości powietrza dostarczanego do systemu; zanieczyszczenia mogą prowadzić do szybszego zużycia komponentów oraz obniżenia efektywności działania. Filtry powietrza powinny być regularnie czyszczone lub wymieniane, aby zapewnić optymalne warunki pracy. Dodatkowo, zawory sterujące wymagają okresowej kontroli pod kątem szczelności oraz sprawności działania; nieszczelności mogą prowadzić do strat energii oraz obniżenia wydajności całego systemu. Nie można zapominać o smarowaniu ruchomych części siłowników pneumatycznych, co pozwala na płynne działanie i zmniejsza tarcie.
Jakie są najczęstsze problemy związane z maszynami pneumatycznymi
Maszyny pneumatyczne, mimo swojej niezawodności, mogą napotykać różnorodne problemy podczas eksploatacji. Jednym z najczęstszych kłopotów jest spadek ciśnienia sprężonego powietrza w systemie, co może prowadzić do obniżenia wydajności urządzeń. Przyczyną tego stanu rzeczy mogą być nieszczelności w przewodach lub zaworach, które należy szybko zidentyfikować i usunąć. Innym powszechnym problemem są zatory w układzie pneumatycznym spowodowane zanieczyszczeniami lub wilgocią w sprężonym powietrzu; takie sytuacje mogą prowadzić do uszkodzenia komponentów oraz przestojów w produkcji. Warto również zwrócić uwagę na hałas generowany przez maszyny pneumatyczne; nadmierny hałas może świadczyć o problemach z łożyskami lub innymi elementami mechanicznymi, które wymagają natychmiastowej interwencji. Kolejnym istotnym zagadnieniem są awarie siłowników pneumatycznych, które mogą występować z powodu niewłaściwego smarowania lub zużycia uszczelek.
Jakie są kluczowe aspekty projektowania maszyn pneumatycznych
Projektowanie maszyn pneumatycznych to proces wymagający uwzględnienia wielu kluczowych aspektów technicznych oraz użytkowych. Na początku należy określić wymagania dotyczące wydajności i funkcjonalności maszyny; to pozwoli na dobór odpowiednich komponentów oraz technologii. Istotnym elementem jest również analiza warunków pracy; maszyna musi być dostosowana do specyfiki środowiska, w którym będzie eksploatowana. Kolejnym krokiem jest wybór odpowiednich materiałów konstrukcyjnych; powinny one charakteryzować się wysoką odpornością na korozję oraz uszkodzenia mechaniczne, co zapewni długowieczność urządzenia. Warto również zwrócić uwagę na ergonomię projektu; operatorzy muszą mieć łatwy dostęp do wszystkich elementów maszyny w celu jej obsługi i konserwacji. Również aspekty związane z bezpieczeństwem mają kluczowe znaczenie; projekt powinien uwzględniać zabezpieczenia przed niekontrolowanym wzrostem ciśnienia czy innymi zagrożeniami związanymi z użyciem sprężonego powietrza.
Jakie są najważniejsze standardy dotyczące maszyn pneumatycznych
W kontekście budowy i eksploatacji maszyn pneumatycznych istnieje szereg standardów oraz norm regulujących ich bezpieczeństwo i efektywność działania. Jednym z najważniejszych dokumentów jest norma ISO 4414 dotycząca systemów pneumatycznych; określa ona zasady projektowania, instalacji oraz użytkowania tych urządzeń w sposób zapewniający bezpieczeństwo operatorów oraz minimalizujący ryzyko awarii. Kolejnym istotnym standardem jest norma EN 983, która dotyczy bezpieczeństwa maszyn i urządzeń wykorzystujących sprężone powietrze; normy te wskazują na konieczność stosowania odpowiednich zabezpieczeń oraz procedur konserwacyjnych. Warto także zwrócić uwagę na normy dotyczące jakości sprężonego powietrza, takie jak ISO 8573; określają one dopuszczalne poziomy zanieczyszczeń oraz wilgoci w sprężonym powietrzu, co ma kluczowe znaczenie dla prawidłowego działania maszyn pneumatycznych.
Jakie są perspektywy rozwoju technologii maszyn pneumatycznych
Technologia maszyn pneumatycznych stale ewoluuje i dostosowuje się do zmieniających się potrzeb rynku przemysłowego. W nadchodzących latach można spodziewać się dalszego rozwoju automatyzacji procesów produkcyjnych poprzez integrację zaawansowanych systemów sterowania opartych na sztucznej inteligencji i analizie danych big data. Tego rodzaju podejście pozwoli na jeszcze lepszą optymalizację pracy maszyn pneumatycznych oraz zwiększenie ich wydajności energetycznej poprzez precyzyjne dostosowanie parametrów pracy do aktualnych potrzeb produkcyjnych. Również rozwój technologii materiałowych przyczyni się do poprawy trwałości i niezawodności komponentów pneumatycznych; nowe materiały będą bardziej odporne na korozję oraz zużycie mechaniczne, co wpłynie na dłuższą żywotność urządzeń. W kontekście ekologii można zauważyć rosnącą tendencję do projektowania bardziej energooszczędnych rozwiązań oraz ograniczenia emisji hałasu generowanego przez maszyny pneumatyczne.